275-243.43: The Essential Seal for Critical Pipe Sealing Needs
The 275-243.43 seal is a critical component for maintaining the integrity and efficiency of mechanical systems across various industries, particularly in automotive and manufacturing sectors. This small yet essential part ensures that machinery operates smoothly, directly impacting both the reliability and longevity of the equipment.
Understanding the value of this seal is vital for professionals tasked with machinery maintenance. A properly functioning seal prevents leaks and protects the system from contamination, resulting in fewer operational disruptions and minimizing equipment downtime. By ensuring the seal is in good condition, businesses can improve performance, reduce repair costs, and extend the lifespan of their machinery. Proper maintenance of such components is key to achieving long-term efficiency and productivity.
Significance of the 275-243.43 Seal in Mechanical Systems
The 275-243.43 seal is an essential component in various mechanical systems, serving a crucial role across multiple industries, including automotive, manufacturing, and water treatment. Its primary function is to maintain the integrity of equipment by preventing leaks and contamination, which can lead to operational failures or compromised performance. By ensuring reliable sealing, this seal contributes to the overall efficiency and longevity of machinery, making it indispensable in many applications.
Key Characteristics of the 275-243.43 Seal
The 275-243.43 seal is integral to the LINK-SEAL® Modular Pipe Sealing System, significantly enhancing its performance and versatility. Designed to withstand pressures up to 20 psig, equivalent to approximately 40 feet of head, and capable of operating in temperatures as high as 175°F, this seal proves its worth across a range of challenging environments.
One of the most notable features of the 275-243.43 seal is its exceptional durability. Engineered to resist degradation from environmental factors, such as ozone, sunlight, water, and a diverse range of chemicals, this seal not only extends its lifespan but also ensures reliability even in adverse conditions. As industries increasingly seek solutions that can withstand harsh operational environments, the 275-243.43 seal stands out as a reliable option.
Material Options for Specific Applications
The 275-243.43 seal is available in various materials to meet specific application requirements. Some of the most common options include:
- Standard EPDM Rubber (Black): Ideal for general use, providing a good balance of durability and flexibility.
- Nitrile Rubber (Green): Offers enhanced resistance to oil and other hydrocarbons, making it suitable for applications where oil exposure is likely.
- Silicone Rubber (Gray): Known for its superior temperature resilience, this material is suitable for high-temperature environments.
- Low Durometer EPDM Rubber (Blue): Designed for delicate piping systems, this option provides a softer sealing solution that minimizes the risk of damage.
These material choices ensure that the 275-243.43 seal can meet the demands of various industrial environments, allowing it to perform reliably across a spectrum of conditions.
Advanced Sealing Mechanisms
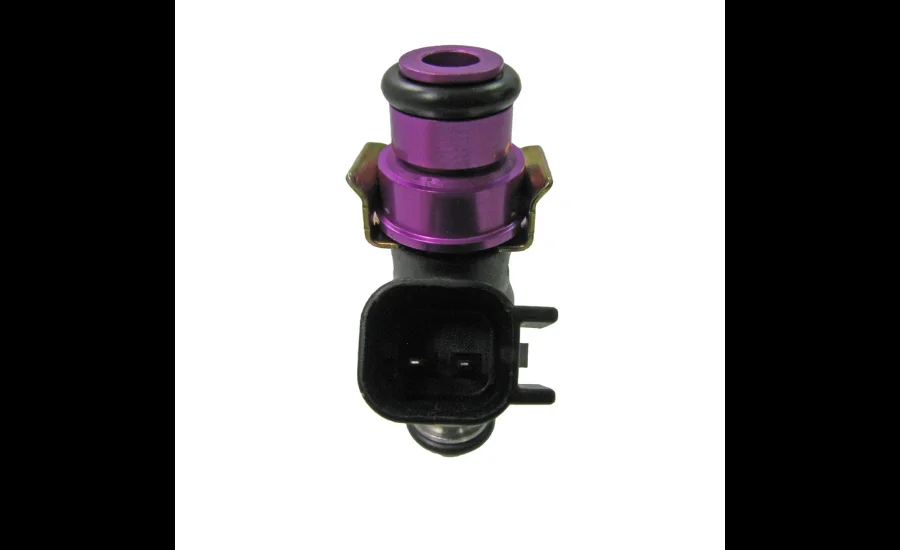
The 275-243.43 seal operates on the principle of modular pipe sealing, a system that integrates individual rubber sealing elements arranged in a circular pattern around a pipe or conduit. This design ensures an extremely tight seal, especially in high-pressure environments where a minimal leakage rate is crucial.
Unlike simple gasket seals or O-rings, this type of seal uses a radial compression system. The rubber elements are compressed as they are tightened, pressing firmly against the pipe wall and sealing any gaps. This compression creates a watertight and airtight barrier, which is especially beneficial in systems where liquids or gases are being transported under pressure.
An innovative feature of the 275-243.43 seal is its capacity to maintain sealing even under dynamic conditions, where the pipes might experience vibration, slight movements, or thermal expansion and contraction. The elasticity of the rubber materials allows the seal to adjust and retain its integrity, even as the mechanical system undergoes stress or fluctuates in operational conditions.
Specialized Seal Design Features
- Multi-layered Sealing Structure: The 275-243.43 seal is not just a single layer of rubber. It often consists of multiple layers of elastomeric materials designed to handle various stresses simultaneously. Each layer has a specific function, such as one layer to provide flexibility, another for heat resistance, and another for pressure retention. This multi-layered structure enhances both the durability and reliability of the seal.
- Groove Designs and Sealing Beads: A distinctive feature of this seal is the inclusion of engineered grooves and sealing beads. These design elements allow the rubber to better grip the surface of the pipe or structure, creating a more secure seal. The grooves also act as channels for any slight leakage that might occur during extreme pressure changes, guiding it back towards the pipe and preventing further escape.
- Spring-Loaded Design: Some variations of the 275-243.43 seal incorporate a spring-loaded mechanism. This involves a metal spring embedded within the rubber material that enhances the force exerted on the pipe, maintaining the seal under varying pressure conditions. The spring ensures constant pressure, compensating for any slight changes in pipe diameter due to thermal expansion.
- Bolt-Tightening Mechanism: Another crucial design feature is the bolt-tightening system. This allows for the radial compression of the seal to be precisely controlled. Each bolt adjusts the pressure evenly around the circumference of the seal, ensuring uniform sealing pressure and reducing the likelihood of weak points developing. This controlled tightening also ensures that the seal is not over-compressed, which could lead to premature wear or failure.
Advanced Material Science: The Role of Elastomers
The 275-243.43 seal is designed with advanced elastomers that offer superior performance in diverse operating environments. Elastomers, a class of polymers with high elasticity, are key to the performance of the seal. The choice of elastomer is tailored to the application:
- Ethylene Propylene Diene Monomer (EPDM):
- Chemical Resistance: EPDM rubber is highly resistant to a wide range of chemicals, including acids, alkalis, and salts. This makes it a perfect choice for applications in industries like wastewater treatment, where exposure to harsh chemicals is common.
- Temperature Tolerance: EPDM is known for its ability to withstand temperatures ranging from -40°F to 300°F, making it ideal for both low-temperature cryogenic applications and high-heat industrial systems.
- Aging and Weather Resistance: EPDM is particularly resistant to aging factors like UV radiation and ozone exposure, which is crucial for outdoor installations and applications where the seal might be exposed to harsh environmental conditions.
- Nitrile Rubber (NBR):
- Hydrocarbon Resistance: Nitrile rubber is prized for its superior resistance to oils and hydrocarbons, making it the preferred material in applications where the seal may come into contact with lubricants, fuels, or other oil-based substances.
- Thermal Stability: While nitrile rubber offers solid resistance to oils, it also handles moderate temperature ranges, making it a versatile material for various industrial uses.
- Silicone Rubber:
- High-Temperature Resilience: Silicone rubber stands out due to its ability to withstand extreme temperatures, from as low as -65°F to as high as 500°F. This makes it particularly valuable in applications involving high heat or where temperature cycling is present.
- Medical and Food-Grade Options: Silicone is often chosen for applications in the medical, pharmaceutical, and food industries because it can be formulated to meet FDA requirements and other regulatory standards for contact with consumables.
- Viton (FKM):
- Superior Chemical Resistance: Viton seals are chosen for highly aggressive chemical environments, such as those found in the oil and gas industry, due to their exceptional resistance to a wide variety of chemicals, including fuels, solvents, and corrosive fluids.
- Extreme Conditions: Viton can handle temperatures up to 400°F, maintaining its integrity in both extreme heat and aggressive chemical exposure environments.
Industry Standards and Certifications
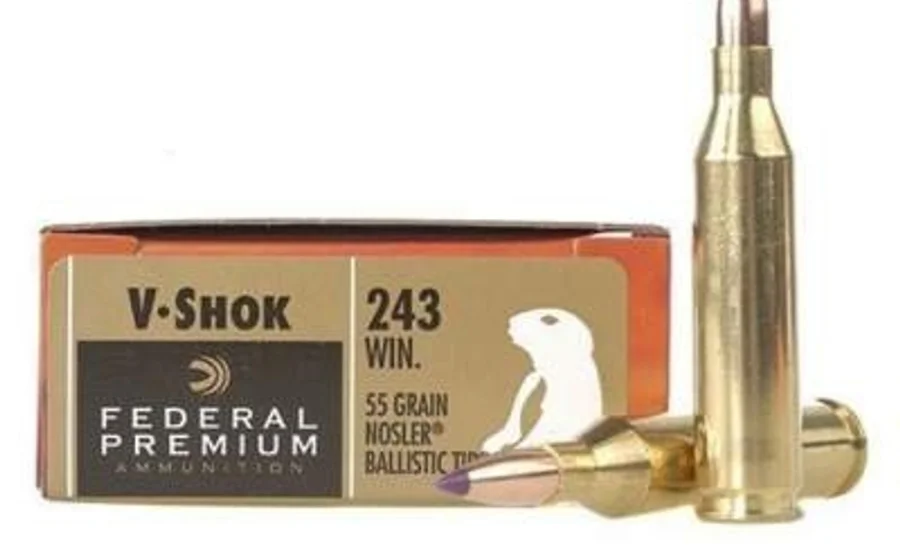
The 275-243.43 seal conforms to numerous international standards that regulate quality, safety, and performance. Some notable certifications include:
- ISO 9001: This seal is manufactured in facilities that adhere to ISO 9001 standards, ensuring consistent quality in production processes and materials. This certification is crucial for industries requiring a high level of reliability and traceability in their equipment.
- ASTM D2000: Elastomeric materials used in the 275-243.43 seal meet ASTM D2000 specifications, which outline the physical properties of rubber materials, including tensile strength, elongation, hardness, and temperature range.
- UL Listings: The seal may carry Underwriters Laboratories (UL) listings, signifying that it has been tested for specific safety standards in fire protection applications, particularly for sealing pipe penetrations through fire-rated walls and floors.
Application-Specific Examples
- Oil & Gas Industry: The 275-243.43 seal is often used in high-pressure pipelines transporting crude oil and natural gas. Its robust chemical resistance to hydrocarbons, coupled with its ability to maintain a tight seal under extreme temperatures and pressures, makes it indispensable for sealing pipe joints and penetrations in refineries and offshore platforms.
- Water Treatment and Wastewater Management: In these industries, the seal plays a vital role in preventing contamination between different water flows. It ensures that pipes passing through barriers remain sealed against both water and wastewater. The seal’s resistance to chlorine and other water treatment chemicals ensures long service life in these environments.
- Power Generation (Nuclear and Thermal Plants): Power plants, particularly nuclear facilities, require seals that can withstand radiation, high pressures, and extreme temperatures. The 275-243.43 seal is utilized in systems where safety is paramount, ensuring that pipe penetrations remain sealed to prevent leaks in hazardous environments.
- Pharmaceutical and Food Processing: In food and pharmaceutical processing plants, the use of FDA-compliant materials, such as silicone or certain grades of EPDM, ensures that the 275-243.43 seal meets hygiene and safety standards. The seal’s chemical resistance also prevents contamination from cleaning agents and sterilization chemicals used in these environments.
Benefits of Using OEM 275-243.43 Seals
Opting for an Original Equipment Manufacturer (OEM) seal, such as the 275-243.43, is crucial for maximizing the performance and longevity of your equipment. Unlike generic or aftermarket seals, OEM seals are specifically designed to meet the exact specifications of your machinery. This guarantees a precise fit, which is vital for maintaining optimal performance and reducing the risk of leaks or failures.
OEM seals undergo rigorous testing to ensure they meet high standards of quality and durability. By investing in a genuine OEM seal, you enhance the reliability of your machinery, which can lead to significant reductions in maintenance costs and unplanned downtime.
Impact on Equipment Performance
Utilizing the appropriate OEM 275-243.43 seal has a direct and positive impact on equipment performance. These seals are engineered with specific considerations for operating conditions, such as pressure, temperature, and lubricant compatibility.
For instance, the ability to withstand temperatures of up to 175°F ensures that the seal can perform effectively in various environments, whether in a heating system or a high-temperature industrial setting. This precise engineering ensures that your machinery operates efficiently, ultimately extending its life span and reducing the likelihood of catastrophic failures.
Extending Machinery Lifespan
The use of high-quality OEM seals, like the 275-243.43, plays a vital role in extending the lifespan of machinery. Manufactured from durable materials, these seals resist degradation caused by exposure to environmental factors such as chemicals, moisture, and extreme temperatures.
Investing in OEM seals safeguards equipment against premature wear and tear. Non-OEM or makeshift alternatives may be less expensive initially but can lead to increased operational costs due to frequent replacements and the potential for further damage to machinery. Therefore, OEM seals are often a wiser long-term investment, ensuring optimal performance and extending the service life of your equipment.
Proper Installation of the 275-243.43 Seal
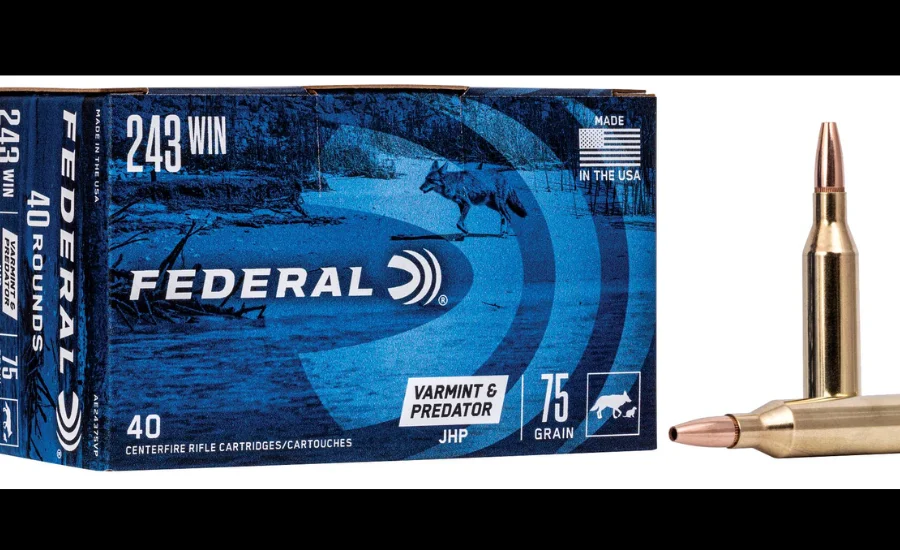
Correct installation is paramount for maximizing the performance of the 275-243.43 seal. The installation process requires careful attention to detail to avoid misalignment or deformation that could compromise sealing effectiveness.
Here are some essential installation tips:
- Ensure Proper Alignment: The seal must be correctly aligned during installation to prevent uneven wear or leakage. Misalignment can lead to significant operational problems over time.
- Clean the Installation Area: Thoroughly clean the bore before installation. Removing debris helps ensure a proper fit and prevents contaminants from compromising the seal’s effectiveness.
- Use Appropriate Tools: Select the correct driving ring size and material to avoid deforming the seal during installation. Accurate alignment of tools is crucial for preventing damage.
- Handle Springs Carefully: Be cautious with the spring located at the back of the seal. Applying a super sticky grease can help keep it in place during the installation process.
By following these guidelines, you can ensure a successful installation of the 275-243.43 seal, thereby enhancing its effectiveness and longevity.
Maintenance for Optimal Performance
Regular maintenance of the 275-243.43 seal is critical for ensuring optimal performance and extending its lifespan. Establishing a routine inspection schedule is essential for catching potential issues early and preventing unexpected failures.
- Visual Inspections: Regularly inspect the seal for signs of wear, such as leaks or irregular wear patterns. Early detection of these signs can save you from costly repairs down the line.
- Lubrication Checks: Ensure that the seal and surrounding components are adequately lubricated. Insufficient lubrication can lead to increased friction and premature failure.
- Monitor Operating Conditions: Keeping track of pressure and temperature levels allows you to identify any deviations from normal parameters, which could indicate underlying issues.
- Cleaning Routine: Develop a cleaning routine using compatible solutions and soft brushes to keep the seal free from debris that could compromise its effectiveness.
By implementing these maintenance practices, you can significantly enhance the reliability and efficiency of your equipment, minimizing the risk of unexpected downtimes.
Choosing Between OEM and Aftermarket Seals
When selecting a seal for the 275-243.43, the decision between OEM and aftermarket options is crucial. OEM seals are designed to meet the original specifications of your machinery, ensuring a precise fit and optimal performance. They undergo rigorous quality control processes, guaranteeing reliability and durability.
In contrast, aftermarket seals may offer a more affordable option but often come with risks related to quality and compatibility. While some aftermarket options can adequately serve their purpose, they may not meet the same stringent standards as OEM seals. This discrepancy can result in premature failures or increased maintenance requirements.
Ultimately, the choice between OEM and aftermarket seals should be guided by your specific operational needs and priorities. Investing in an OEM seal is generally the safer bet for ensuring superior quality and compatibility, while aftermarket seals may present cost advantages but could lead to performance issues.
Long-Term Cost Considerations
When evaluating seals for the 275-243.43, it’s essential to consider both upfront costs and long-term value. Although OEM seals typically have a higher initial purchase price, their guaranteed quality and precise fit can lead to fewer replacements and lower maintenance costs over time.
Aftermarket seals may appear cheaper, but their durability can be inconsistent. A lower-quality aftermarket seal that fails prematurely could lead to increased costs due to frequent replacements and potential damage to other machinery components. This can result in extended downtimes and repair expenses, ultimately diminishing the initial savings.
Online Availability and Pricing
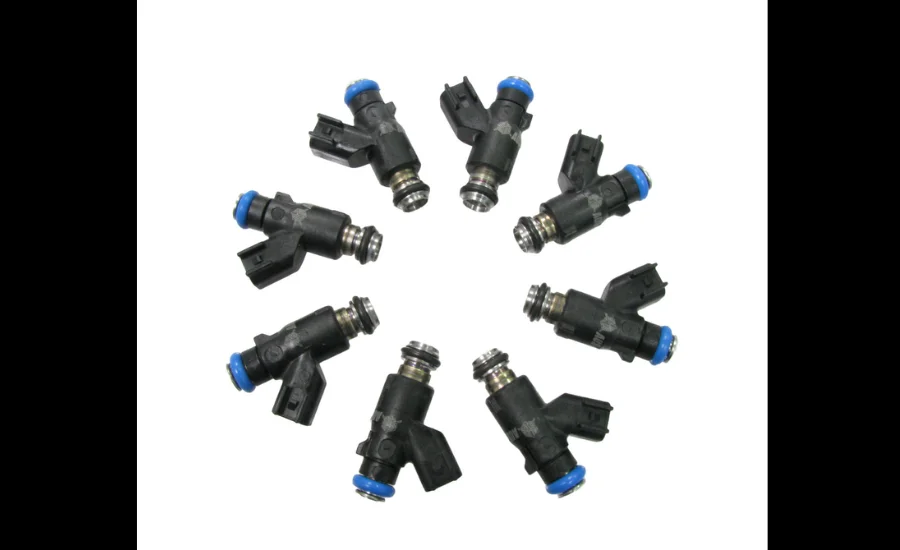
The 275-243.43 seal is widely available through various online platforms, making it easy to source. Pricing can vary depending on the retailer and specific requirements of your equipment. When shopping online, it’s essential to verify the authenticity of the part and ensure compatibility with your machinery.
While aftermarket options may offer a lower price point, investing in an OEM seal ensures superior performance and reliability. Many reputable online retailers provide the option for same-day shipping, which can be crucial if you require the part quickly for maintenance or repairs.
Also Read: Asotecnicos del Cesar Valledupar
Final Words
The 275-243.43 seal is a critical component in mechanical systems, providing reliable sealing in industries like automotive, manufacturing, and water treatment. Its role in preventing leaks and contamination directly impacts the efficiency and lifespan of machinery, ensuring smooth operation and minimizing downtime. The seal’s durability is enhanced by its resistance to environmental factors such as chemicals, temperature fluctuations, and wear.
Available in various materials, including EPDM, nitrile, and silicone rubber, the 275-243.43 seal meets specific application needs. Its advanced sealing mechanisms, such as modular pipe sealing and bolt-tightening systems, ensure an airtight, watertight seal even under pressure. Choosing OEM versions ensures superior quality and performance, extending equipment life and reducing maintenance costs. Proper installation and regular maintenance are key to optimizing the seal’s effectiveness.
For exclusive offers and industry insights, trust Washington Breeze to keep your machinery running smoothly and efficiently.